text.skipToContent
text.skipToNavigation
La fusion de l’aluminium nécessite de casser une couche épaisse de cryolite, plusieurs fois d’affilée, à des températures élevées. Par conséquent, pour Damco Aluminium Delfzijl Coöperatie (Aldel), l’utilisation d’un cylindre ordinaire n’était pas une option. Et cela contrastait avec le nouveau casse-croûte. Conçu par IMI Norgren et fourni par itsme, ce cylindre durera plusieurs années tout en étant adapté à de nombreuses fissions.
Environ quatre-vingts fours. Un nombre plus élevé de fours n’était pas en fonction lorsqu’André van der Ploeg a commencé à travailler pour Damco Aluminium Delfzijl Coöperatie (Aldel). La société sortait juste d’une faillite et les processus étaient minutieusement remis en marche. Et maintenant, regardez : à peine deux ans plus tard, 230 des 304 fours au total fonctionnent. Répartis sur plus de deux halls gigantesques, ils assurent la production d’aluminium liquide qui, une fois solidifié, est utilisé dans les industries, dans le pays et à l’étranger.
Il ne serait pas étonnant si André et ses collègues utilisaient la totalité des 304 fours très prochainement. « Notre société s’est considérablement développée et continue sur sa lancée. Lorsque j’ai commencé ici, nous employions 170 personnes de façon permanente. Aujourd’hui heureusement, nous avons doublé cet effectif », a indiqué André.
Ici, à Farnsum, dans la municipalité de Delfzijl, au nord-est de Groningen, une société comme Aldel est un employeur majeur en termes d’emploi régional. André travaille pour le fabricant d’aluminium en qualité de gestionnaire des biens, responsable de l’intégrité, de la disponibilité et de la maintenance (préventive et corrective) des installations dans les deux halls géants.
Il décrit son emploi comme un travail passionnant. « Dans ces halls, tout est question de livrer de l’aluminium liquide à notre fonderie. Et c’est un processus continu qui implique beaucoup de travail. »
L’ajout d’alumine de façon aléatoire n’a aucun sens, précise André. La matière première doit être poussée à travers la croûte de cryolite. Dans chaque four, cela se fait par deux cylindres qui cassent la croûte un nombre de fois incalculable.
« Toutes les 24 heures, nous ajoutons deux tonnes d’alumine dans le contenu d’un four. Nous le faisons par doses de deux kilos chacune, ce qui signifie que chaque cylindre casse la croûte plus de vingt fois en une heure. »
Les cylindres actuels dans les fours d’Aldel fonctionnent mais sont obsolètes. Lors d’un nouveau démarrage, la maintenance s’est révélée urgente, mais la révision exigeait d’André et de ses collègues des capacités de résolution de problèmes. « Nous ne produisions plus nos cylindres actuels. Nous en avions heureusement en stock et nous pouvons également utiliser les parties de cylindre des fours qui sont toujours à l’arrêt. Mais c’est une solution temporaire. Surtout maintenant, puisque nous allons utiliser encore plus de fours. » André devait alors chercher un nouveau cylindre. Un contact direct avec un fabricant paraissait peut-être évident mais André n’était guère ravi à cette idée. « Comment pourrais-je être certain que nous obtiendrions la meilleure solution ? J’ai choisi la sûreté. J’ai par conséquent contacté itsme tout naturellement avec qui nous travaillons depuis de nombreuses années. itsme nous soutient au niveau de l’ingénierie électrique et de la mécanique, nous livre rapidement et n’est pas affiliée à des marques. Et ce dernier point était particulièrement pertinent pour notre demande. »
Par conséquent, André a reçu plusieurs offres l’an passé de Herbert Sturing, spécialiste du marketing en services de produits pneumatiques chez itsme. Et cela à la suite d’un minutieux processus de sélection, a indiqué Herbert. « Nous n’avons pas simplement choisi des marques au hasard mais avons fait une sélection réfléchie en fonction des besoins d’Aldel. Chez itsme, c’est notre domaine en termes de pneumatiques et nous disposons du savoir-faire pour esquisser une ébauche complète des possibilités. C’est cela qui garantit une relation optimale entre le client et le fabricant. »
Parmi les trois suggestions, celle d’IMI Norgren s’est révélée être la meilleure. Notamment en raison de la conception détaillée, mais selon André, en raison également de l’expérience d’IMI Norgren avec ce type de cylindre. « La société ne laisse rien au hasard et cela a été confirmé également pour ce projet. Tout comme Herbert, Erik de Jager de Norgren était présent régulièrement et ensemble, nous avons trouvé la bonne solution. Toutes les personnes impliquées ont consacré beaucoup de temps et d’énergie dans ce projet. Et nous avons réussi. »
Pour l’heure, cela concerne uniquement une version du cylindre Norgren. Avec un poids de presque quatre-vingts kilos, un piston de vingt centimètres de diamètre et une course de soixante-dix centimètres, le casse-croûte est utilisé à plein régime depuis la fin de l’été 2019, à la grande satisfaction d’André. « Le cylindre fonctionne à la perfection. Pour nous, c’est le point de départ. À partir d’aujourd’hui, nous savons quel cylindre acheter. Car pour nous, il est clair que nous ne nous arrêterons pas là. »
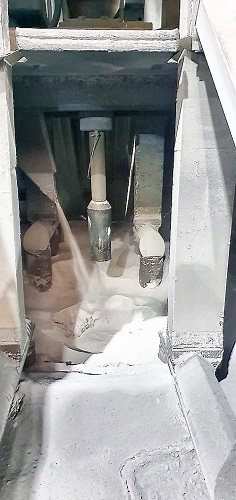
VIGOUREUSEMENT À TRAVERS LA CRYOLITE
Le casse-croûte d’IMI Norgren réussit le test à Aldel
La fusion de l’aluminium nécessite de casser une couche épaisse de cryolite, plusieurs fois d’affilée, à des températures élevées. Par conséquent, pour Damco Aluminium Delfzijl Coöperatie (Aldel), l’utilisation d’un cylindre ordinaire n’était pas une option. Et cela contrastait avec le nouveau casse-croûte. Conçu par IMI Norgren et fourni par itsme, ce cylindre durera plusieurs années tout en étant adapté à de nombreuses fissions.Environ quatre-vingts fours. Un nombre plus élevé de fours n’était pas en fonction lorsqu’André van der Ploeg a commencé à travailler pour Damco Aluminium Delfzijl Coöperatie (Aldel). La société sortait juste d’une faillite et les processus étaient minutieusement remis en marche. Et maintenant, regardez : à peine deux ans plus tard, 230 des 304 fours au total fonctionnent. Répartis sur plus de deux halls gigantesques, ils assurent la production d’aluminium liquide qui, une fois solidifié, est utilisé dans les industries, dans le pays et à l’étranger.
Il ne serait pas étonnant si André et ses collègues utilisaient la totalité des 304 fours très prochainement. « Notre société s’est considérablement développée et continue sur sa lancée. Lorsque j’ai commencé ici, nous employions 170 personnes de façon permanente. Aujourd’hui heureusement, nous avons doublé cet effectif », a indiqué André.
Ici, à Farnsum, dans la municipalité de Delfzijl, au nord-est de Groningen, une société comme Aldel est un employeur majeur en termes d’emploi régional. André travaille pour le fabricant d’aluminium en qualité de gestionnaire des biens, responsable de l’intégrité, de la disponibilité et de la maintenance (préventive et corrective) des installations dans les deux halls géants.
Il décrit son emploi comme un travail passionnant. « Dans ces halls, tout est question de livrer de l’aluminium liquide à notre fonderie. Et c’est un processus continu qui implique beaucoup de travail. »
950 degrés Celsius
La fusion de l’aluminium se fait dans des circonstances particulières. Il ne faut pas oublier que c’est une industrie lourde. Chaque four contient une couche épaisse de cryolite à une température moyenne de 950 degrés Celsius. L’ajout d’alumine donne un aluminium pur grâce à un processus d’électrolyse.« Toutes les 24 heures, deux tonnes d’alumine sont déversées dans un four »
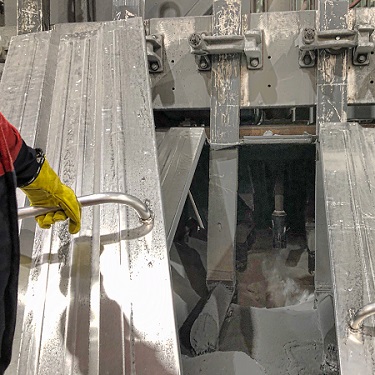
« Toutes les 24 heures, nous ajoutons deux tonnes d’alumine dans le contenu d’un four. Nous le faisons par doses de deux kilos chacune, ce qui signifie que chaque cylindre casse la croûte plus de vingt fois en une heure. »
Il était urgent de se tourner vers la maintenance
Les cylindres actuels dans les fours d’Aldel fonctionnent mais sont obsolètes. Lors d’un nouveau démarrage, la maintenance s’est révélée urgente, mais la révision exigeait d’André et de ses collègues des capacités de résolution de problèmes. « Nous ne produisions plus nos cylindres actuels. Nous en avions heureusement en stock et nous pouvons également utiliser les parties de cylindre des fours qui sont toujours à l’arrêt. Mais c’est une solution temporaire. Surtout maintenant, puisque nous allons utiliser encore plus de fours. » André devait alors chercher un nouveau cylindre. Un contact direct avec un fabricant paraissait peut-être évident mais André n’était guère ravi à cette idée. « Comment pourrais-je être certain que nous obtiendrions la meilleure solution ? J’ai choisi la sûreté. J’ai par conséquent contacté itsme tout naturellement avec qui nous travaillons depuis de nombreuses années. itsme nous soutient au niveau de l’ingénierie électrique et de la mécanique, nous livre rapidement et n’est pas affiliée à des marques. Et ce dernier point était particulièrement pertinent pour notre demande. »
Pas des marques au hasard
Par conséquent, André a reçu plusieurs offres l’an passé de Herbert Sturing, spécialiste du marketing en services de produits pneumatiques chez itsme. Et cela à la suite d’un minutieux processus de sélection, a indiqué Herbert. « Nous n’avons pas simplement choisi des marques au hasard mais avons fait une sélection réfléchie en fonction des besoins d’Aldel. Chez itsme, c’est notre domaine en termes de pneumatiques et nous disposons du savoir-faire pour esquisser une ébauche complète des possibilités. C’est cela qui garantit une relation optimale entre le client et le fabricant. »
« Nous y avons consacré beaucoup de temps et d’énergie et cela a abouti. »

Pour l’heure, cela concerne uniquement une version du cylindre Norgren. Avec un poids de presque quatre-vingts kilos, un piston de vingt centimètres de diamètre et une course de soixante-dix centimètres, le casse-croûte est utilisé à plein régime depuis la fin de l’été 2019, à la grande satisfaction d’André. « Le cylindre fonctionne à la perfection. Pour nous, c’est le point de départ. À partir d’aujourd’hui, nous savons quel cylindre acheter. Car pour nous, il est clair que nous ne nous arrêterons pas là. »
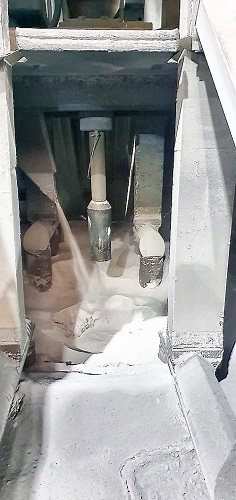
Question de confianceDes processus industriels lourds : c’est le monde d’IMI Norgren qui, à la fin de l’an dernier, a fourni à Aldel un casse-croûte robuste. Erick de Jager, ingénieur des ventes à IMI Norgren repense au processus avec joie. « En définitive, tout est une question de confiance. La confiance dans le savoir-faire de chacun, mais également dans le respect des engagements. Dans ce projet, nous étions un prolongement d’itsme sous la direction d’Aldel. Et cela a bien marché. Le cylindre fonctionne comme il le devrait. Une chose est sûre, Adel peut aller de l’avant. » |
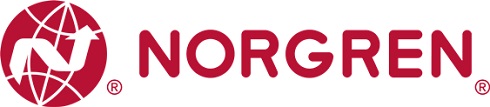
S’effondrer, tenir debout et prendre le virage de l’écologieL’histoire de Damco Aluminium Delfzijl Coöperatie (Aldel) est pleine de rebondissements. Depuis sa création en 1966, la société a connu de multiples faillites et rachats. Dans l’intervalle, le virage vers l’écologie joue un rôle très important chez Aldel, par exemple avec l’installation de deux halls de production équipés de 50 000 mètres carrés de panneaux solaires. Une réduction des émissions de CO², une utilisation accrue de l’énergie durable : l’avenir d’Aldel est tout simplement aussi rose qu’il est vert. |
Peut-être vous êtes aussi intéressé par ceci
Réingénierie pneumatique
Lire plus
Notre réingénierie de votre système pneumatique commence par un inventaire. Nous examinons d'abord le compresseur. Ensuite, nous vérifions également le réseau de tuyauterie, les raccords et les tuyaux nécessaires à la commande des composants pneumatiques. Si certains composants doivent être remplacés par de nouvelles versions, cela est mentionné dans le rapport.
Support technique
Lire plus
itsme Industrial Automation connaît votre univers. Ce ne sont pas que des mots, nous le prouvons chaque jour. Lorsque nous venons chez vous, nous n’attendons pas, mais itsme Industrial Automation connaît votre univers. Ce ne sont pas que des mots, nous le prouvons chaque jour. Lorsque nous venons chez vous, nous n’attendons pas, nous prenons des mesures et nous travaillons pour vous. C’est cette proactivité qui nous caractérise. Et cela fonctionne, nos services d’assistance technique le démontrent.